What is simple costing system? Traditional costing is the allocation of factory overhead to products based on the volume of production resources consumed. Under this method , overhead is usually applied based on either the amount of direct labor hours consumed or machine hours used.
Full Answer
What are the types of costing systems?
- Fixed Cost – It is the cost of fixed inputs used in production.
- Variable Cost – It is the cost of variable inputs used in production.
- Semi Variable Cost – It refers to costs which are partly fixed and partly variable.
- Total Cost – It refers to the total cost of production.
What is a traditional costing system?
The traditional costing system is an accounting method used to determine the cost of making products to make a profit, and it is based on allocating overhead (or indirect) manufacturing costs. This system relies on calculating predetermined overhead rates and applying the rates to a given metric.
How to implement a cost accounting system?
To calculate implementation costs, you need to:
- Elect a team leader to head up your steering committee and build a team to help with the key decisions
- Create a requirements list (features, integrations, users, cloud or on-premise)
- Send out an RFI to the vendors you feel are the best fit
- Shortlist the vendors and request proposals
What are the different types of costing methods?
- Method # 1. Job Costing: Under this method, costs are collected, accumulated and ascertained for each job separately. ...
- Method # 2. Process Costing: This method is suitable to industries where production is undertaken on mass scale and on continuous basis.
- Method # 3. ...
How do you do simple costing?
1:534:21Activity-based Costing - Simple Costing versus ABC - YouTubeYouTubeStart of suggested clipEnd of suggested clipSo just to recap remember simple costing we allocate one rate in this case we had one allocationMoreSo just to recap remember simple costing we allocate one rate in this case we had one allocation base and that was direct labor-hours.
What do you mean by costing system?
A costing system is designed to monitor the costs incurred by a business. The system is comprised of a set of forms, processes, controls, and reports that are designed to aggregate and report to management about revenues, costs, and profitability.Nov 18, 2021
What is ABC system?
Activity-based costing (ABC) is a method of assigning overhead and indirect costs—such as salaries and utilities—to products and services. The ABC system of cost accounting is based on activities, which are considered any event, unit of work, or task with a specific goal.
What is costing system with examples?
It is appropriate for products whose production is a process involving different departments and costs flow from one department to another. For example, it is the cost accounting system used by oil refineries, chemical producers, etc.Jun 18, 2013
What are the types of costing system?
The main costing methods available are process costing, job costing and direct costing. Each of these methods apply to different production and decision environments.Sep 24, 2017
What is the important of costing system?
The costing system provides information that is useful to managers for minimizing wastage and allocating resources to different departments. The traditional costing system is a costing system which calculates a single overhead rate and applies it to each job or department.
What is ABC costing PDF?
Activity-based costing (ABC) is a method, which identifies activities in a firm and assigns the expenses of each activity with resources to all products and services based on the real consumption by each. This method allocates more overhead costs into direct expenses compared with conventional method.
Is ABC better than traditional costing?
The differences are in the accuracy and complexity of the two methods. Traditional costing is more simplistic and less accurate than ABC, and typically assigns overhead costs to products based on an arbitrary average rate. ABC is more complex and more accurate than traditional costing.
How do you calculate ABC costing?
Activity-based costing (ABC) is a method to determine the total cost of manufacturing a product, including overhead. It is calculated by taking the cost pool total and dividing it by the cost driver.Oct 7, 2021
What are the 4 types of costing?
Direct, indirect, fixed, and variable are the 4 main kinds of cost.Oct 8, 2020
What are the 4 types of cost accounting?
There are mainly four types of cost accounting: standard cost accounting, activity based accounting, lean accounting and marginal costing.
What is the primary costing system?
The primary costing systems are: Job costing system. Materials, labor, and overhead costs are compiled for an individual unit or job.
What are the different types of costing systems?
There are two main types of costing systems. A business can accumulate information based on either one, or adopt a hybrid approach that mixes and matches systems to best meet its needs. The primary costing systems are: 1 Job costing system. Materials, labor, and overhead costs are compiled for an individual unit or job. This approach works best for unique products, such as custom-designed machines or consulting projects. The cost accumulation process is highly detailed and labor-intensive. 2 Process costing system. Materials, labor and overhead costs are compiled in aggregate for an entire production process, and are then allocated to individual production units. This approach works well for large production runs of identical items, such as a production run of 100,000 cell phones. The cost accumulation process is highly efficient and portions of it can possibly be automated.
What is process costing?
Process costing system. Materials, labor and overhead costs are compiled in aggregate for an entire production process, and are then allocated to individual production units. This approach works well for large production runs of identical items, such as a production run of 100,000 cell phones. The cost accumulation process is highly efficient and portions of it can possibly be automated.
What is simple food cost?
Your simple food cost is made up of your actual sales mix, meaning, what you sold of each menu item at a given day, times your theoretical menu item cost that we performed in the simple food cost program.
Why is simple food costing important?
What is Simple Food Costing and Why is it Important? Simple Food Costing Tool is like a heart monitor for your business. Sometimes you’re not aware of issues until it’s too late. By monitoring your costs, which is basically when you got high blood pressure, you need a heart monitor to monitor.
How to calculate food cost percentage?
So you take the food cost in dollars, divide it by the net sales, and that will give you your actual food cost percentage. Then you subtract out the expected food cost percentage, and you’re expected food cost percentage is calculated by your simple food cost divided by net sales.
What are the three aspects of food costing?
There are three important aspects to food costing: 1. Price . 2. Recipe mix. 3. Tracking. The menu item pricing of course is the owner’s responsibility to go out in the marketplace, and determine the competitor’s pricing, what the market can bear and to adjust those prices accordingly to remain competitive.
Why is it important to understand food costing?
So again, the benefit of understanding and implementing food costing is that it creates an awareness of exactly where the price, the recipe mix, and what the results are generating from every action that you put into the menu.
How to find food cost percentage in QuickBooks?
To get their food cost percentage, most owners I know just look at their QuickBooks to their profit and loss, and take what they bought in a month, and they divide that by total sales, which may or may not include sales tax . One major item of note: I want to teach an operator that food cost does not equal total food purchases divided by total unit sales.
What is standard costing?
Under standard costing system, the ascertainment and use of standard costs and the measurement and analysis of variances is done for control purpose. Standard cost is a predetermined cost which is computed in advance of production on the basis of a specification of all the factors affecting costs and used in Standard Costing. Its main purpose is to provide a base for control through Variance Accounting, for valuation of stock and work-in-progress and, in some cases, for fixing selling prices.
What is direct costing?
Direct Costing: It is a method of costing in which the product is charged with only those costs which vary with volume. Variable or direct costs such as direct material, direct labour and variable manufacturing expenses are examples of costs charged to the product.
What is the absorption costing system?
Under the ‘absorption costing system’ all fixed and variable costs are allotted to cost units and total overheads are absorbed according to activity level. In absorption costing system, fixed manufacturing overheads are allocated to products, and these are included in stock valuation.
What is the purpose of historical costing?
The main objective of it is to ascertain costs that have been incurred in past. It is the process of accumulation of costs after they are incurred in a systematic manner. The historical costs are used only for postmortem examination of actual costs incurred and it would be too late to control. The actual figures can be compared only when the standards of performance exists.
What is marginal costing?
Under marginal costing, costs are classified into fixed and variable costs. Variable costs are charged to unit cost and the fixed costs attributable to the relevant period are written-off in full against the contribution for that period.
Is costing a distinct method?
It is not a distinct method of costing. It is the adoption of identical costing principles and procedures by several units of the same industry or several undertakings by mutual agreement. It facilitate valid comparisons between organizations and helps in elimination of inefficiencies.
Is WIP a fixed cost?
Therefore, valuation of inventories of finished goods and WIP includes manufacturing fixed cost and transferred to next period. Unlike manufacturing fixed overhead, the administrative overhead, selling and distribution overheads are treated as fixed cost and recorded only when they incurs. It is a traditional form of cost ascertainment. It is based on the principle that costs should be charged or absorbed to whatever is being costed – be it cost unit, cost centre – on the basis of the benefit received from these costs.
What is process costing?
Process costing accumulates the manufacturing cost separately for all processes. Businesses where the production process involves different departments and cost flows from one department to the other, rely on process costing. For instance, chemical producers, oil refineries and more rely on this type of cost accounting system.
How does cost accounting work?
Basically, a company deploys the cost accounting system to track the raw materials even before the production process begins. Eventually, these raw materials convert into finished goods in real-time. Once the raw materials enter the production, system tracks and record the use of the materials by crediting the raw material account and debiting the goods in the process account.
Why do manufacturers use cost accounting?
Manufacturers use cost accounting systems to keep a tab on the production activities using a perpetual inventory system. In simple words, the cost accounting system is meant for simplifying the work of the manufacturers, who need to track the flow of inventory on a continuous basis through various stages of production.
Why is cost accounting important?
A cost accounting system is important to the executives within the company, such as account manager. The financial accounting results hold more importance for outside parties, such as creditors, investors and government regulators.
Why is costing important in business?
It helps the business to lower the cost of the business operation by identifying and controlling relevant items. Thus, it leads to profit maximization. Costing system also helps in understanding the closing value of materials inventory, work-in-progress and finished goods inventory for preparing the financial statement.
What are the four ways to accumulate costs?
There are four ways to accumulate cost – Job Order, Process, Backflush and Hybrid.
What is cost accounting?
Cost Accounting Systems are useful for all kinds of business, be it manufacturing or trading products, or even a company dealing in services. There are several types of cost accounting systems available for all kinds of businesses. One can choose the best by looking for the one that best allocates costs to manufacture goods. For example, allocating by manufacturing complexity, product lines, production volume, production process and more. Additionally, to ensure the effectiveness of the system, it is crucial that management understands the cost of production and calculate it correctly. 1,2
What is the costing system in accounting?
The traditional costing system in accounting is the allocation of factory overhead to products which is based on the volume of consumed production resources. Companies using this method will apply overhead to either the number of machine hours used or the direct labor hours which were consumed.
What is the traditional costing system?
Under the traditional costing system, you have multiple approaches to consider when looking for the best option to convey information about cost. Your options include volume-based costing, the French cost accounting approach, and planned marginal cost accounting. Each specific system offers advantages and disadvantages to consider, based on the structure of the organization and the number of products which are offered.
How does costing work?
It tends to distort the actual expense, looking at the profitability of products or services by arbitrarily assigning costs for all activities instead of considering the cost of each action required to bring the product to sale.
How to calculate overhead rate?
There are no fancy calculations or forms required to determine the average overhead rate under the traditional costing system. All you must do is calculate the amount of time it takes to produce a specific product or provide a unique service. Then you take the average rate of labor or machine use costs per hour, multiplying it by the length of time necessary to create saleable goods and services.
Why are companies moving away from costing?
Many companies are transitioning away from this accounting option because its accuracy is dependent upon direct costs being high and indirect costs being low. If you’re thinking about moving away from the traditional costing system, there here are its advantages and disadvantages to consider first.
What is non manufacturing cost analysis?
The modern business must analyze non-manufacturing costs as part of their overall accounting process. It must evaluate the vast variety of expenses that are associated with an offer of numerous products or services. You cannot receive that information from the traditional costing system. Although the calculations are easy, and the information is easy to convey to others, the overall lack of data is limiting to organizations which offer numerous items for sale.
Why doesn't the costing system look at marketing, sales, or outreach costs?
The traditional costing system wouldn’t look at marketing, sales, or outreach costs because those occur after the manufacturing process. If those costs are high, then this system might indicate profitability for a company when none exists. Its failure to analyze non-manufacturing costs is one of its greatest weaknesses.
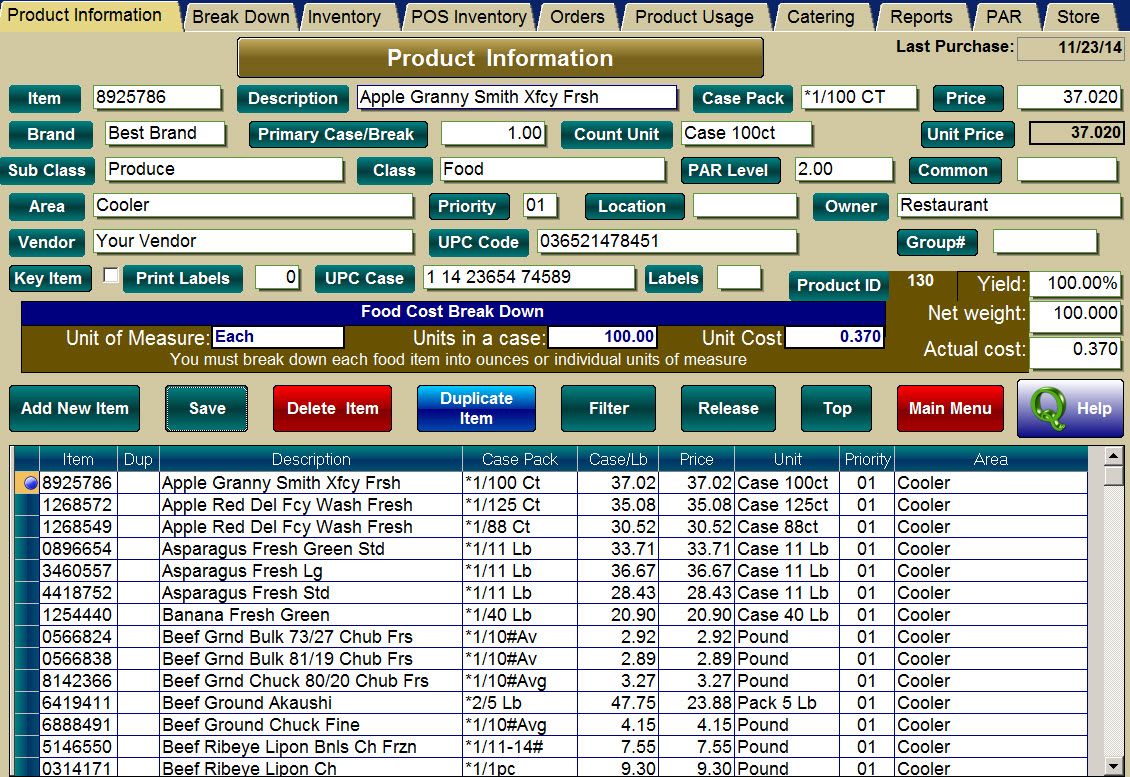