- Process Variable. The process variable is the parameter that is to be controlled. ...
- Sensors or Transducers. Devices that measure process variables are transducers or sensors. ...
- Setpoint. ...
- Control Output or Manipulated Variable. ...
Full Answer
What is a controlled variable in process control?
Controlled Variable – The controlled variable is a process parameter being controlled. In the example here, water level in the tank is the controlled variable, but it can be any process you wish to control. Controlling this variable is the primary function of process control.
What is a process variable?
A process variable, process value or process parameter is the current measured value of a particular part of a process which is being monitored or controlled. An example of this would be the temperature of a furnace. The current temperature is called the process variable, while the desired temperature is known as...
What are the basics of process control?
These are manipulated in the process and a new chemical or component emerges at the output. The controlled inputs to the process and the measured output parameters from the process are called variables Basics of process control. Controlled or measured variable is the monitored output variable from a process.
What are the process variables selected as model input and output?
The process variables selected as model input variables are inlet flue gas flow rate, CO2 concentration in inlet flue gas, pressure of flue gas, temperature of flue gas, lean solvent flow rate, MEA concentration and temperature of lean solvent. The model output is CO 2 capture level.
What is process variable and control variable?
The parameter that is controlled is the Control Variable (CV) The parameter that reacts to a Control Variable change is the Process Variable (PV) The target value for PV is the Setpoint (SP)
What is process variable and types of process variables?
Process Variable Common process variables include – level, flow, temperature, density, PH(acidity or alkalinity), mass, conductivity etc.
What are process variables and examples?
A physical or chemical quantity that is usually measured and controlled in the operation of a water, wastewater, or industrial treatment plant. Common process variables are flow, level, pressure, temperature, turbidity, chlorine, and oxygen levels.
What is the variables involved in process control?
The most common variables controlled are pressure, level, temperature, and flow. Even though there are many different methods used to control these processes, this monitoring and control is generically called process control. Level, pressure, temperature, and flow are all controlled in a similar fashion.
What do you mean by process variables?
A process variable, process value or process parameter is the current measured value of a particular part of a process which is being monitored or controlled. An example of this would be the temperature of a furnace.
What are the 4 process variables?
DAC Worldwide's 4-Variable Advanced Process Control Training System (603-000) is a fully functional, industrial-quality fluid process system that provides hands-on training in the measurement and control of four of the most common process variables: level, pressure, temperature, and flow.
Which one is not a process variable?
Control variable for spray is not a process.
What is a process variable Mcq?
A process parameter that changes value.
What is process variable?
A process variable, process value or process parameter is the current measured value of a particular part of a process which is being monitored or controlled. An example of this would be the temperature of a furnace.
Why is process measurement important?
Measurement of process variables are essential in control systems to controlling a process. The value of the process variable is continuously monitored so that control may be exerted.
What is the difference between the current temperature and the desired temperature?
The current temperature is called the process variable, while the desired temperature is known as the set-point. The set point is usually abbreviated to SP, and the process value is usually abbreviated to PV.
What is SP-PV error?
The SP-PV error is used to exert control on a process so that the value of PV equals the value of the SP. A classic use of this is in the PID controller .
What are the most common variables that are controlled in an industrial process?
The most common variables controlled are pressure, level, temperature, and flow. Even though there are many different methods used to control these processes, this monitoring and control is generically called ...
What is a controlled variable?
Controlled Variable – The controlled variable is a process parameter being controlled. In the example here, water level in the tank is the controlled variable, but it can be any process you wish to control. Controlling this variable is the primary function of process control. Controlled variable is indicated with the letter “c.”
What is a measured variable?
Measured Variable – The measured variable is the electronic or pneumatic representation of the value of the controlled variable. The measured variable typically comes from a transmitter, which measures the controlled variable and produces an output representative of it. In the example here, the level transmitter is measuring level in the tank (the controlled variable) and converting that level to a 4-20 milliamp signal. Measured variable is indicated with the letter “b.”
What is controller output?
Controller Output – The controller output is simply the total output of the controller. With the controller in automatic, the output is calculated by the controller itself. If the controller is placed in manual, the output can be manually adjusted to any desired position. Controller output is indicated with the letter “p.”
How many time constants does a self-regulated process have?
In this example, the process changes by 10%. The time it takes to change 6.32 inches (63.2% of 10 inches), is the time constant. It takes five time constants in order for the process to complete the total change .
How does time affect the process?
The time constant is affected by the capacity of the process and the process’ resistance to change. The larger the process capacity, the longer the time constant, and the more resistive elements in the process (small pipes, penetrations, valves, etc), the longer the time constant.
What type of control is needed to maintain a process?
There are two broad categories of processes: self-regulated processes and non self-regulated processes.
Why are process variables important?
Some process variables are more important than others, in that if they are optimally controlled, they ensure optimal operation of the process (Morari, 1980 ). The decision regarding optimal selection of controlled variables is at a higher level than pairing controlled and manipulated variables. The optimal controlled variable benefits an online optimizing control structure in that maintaining these controlled variables at their setpoints maximizes profitability and minimizes the requirement for setpoint manipulation. In addition, in a control structure with constant setpoint policy, optimal controlled variables induce a self-optimizing framework, ( Skogestad, 2000 ).
What are the input variables for a process?
The process variables selected as model input variables are inlet flue gas flow rate, CO2 concentration in inlet flue gas, pressure of flue gas, temperature of flue gas, lean solvent flow rate, MEA concentration and temperature of lean solvent. The model output is CO 2 capture level. The simulated static process operation data set is divided into training data (50%), testing data (25%) and unseen validation data (25%). Data were scaled to zero mean and unit variance before used for model building. In order to determine the number of hidden neurons required, a number of hidden neurons ranging from 1 to 30 were considered and the ELM with the lowest mean square errors (MSE) on the testing data is considered as having the appropriate number of hidden neurons. Figure 3 shows the MSE values on training data and testing data and unseen validation data of ELM with different numbers of hidden neurons. It can be seen from Figure 3 that ELM with small numbers of hidden neurons (e.g. less than 10) cannot model the relationship adequately with large MSE values on all the three data sets. This is in contrast to conventional neural networks which can give adequate modelling performance with small number of hidden neurons in some cases (Li et al., 2005). This is due to the fact that ELM has randomly assigned input layer weights and a small number of hidden neurons may not be able to establish the underlying nonlinear mapping.
What are the modified process variables?
The modified process variables were related to the number of stages, location of feeds and internal flow division due to the partition wall (in the case of DWC). The own parameters of the DE selected were Cr = 0.8, F = 0.9 for both cases, and Np = 80 and 8,000 simulations for the reference case, and Np = 100 and 9,000 simulations for the DWC. The term Cr stands for the crossover factor, F = mutation factor and Np the population number. Last three rows in Table 2 summarize the main results for the optimal sequences, as well as the percentage of reduction with respect the reference case. According to the data from Table 2, the difference in the energy consumption, the size of the equipment and the TAC were not significantly improved by the optimization from the starting values. However, the alternative DWC configuration moderately outperformed the reference case.
How many process variables are there in UniSim?
The chemical process with 14 process variables simulated by UniSim Design R390.1 includes two CSTRs in series where cold water and hot water are mixed. All of the control loops are proportional controls. The Process Flow Diagram (PFD) is shown in Fig. 3.
What is the theoretical number of stages of the liquid-liquid extraction column (EXT)?
Theoretical number of stages of the liquid-liquid extraction column (EXT): 2-30.
What is the final output variable to be regressed?
The final output variable to be regressed is the total mass fraction of aromatics (sum of all aromatics compound) in the product stream.
Is the inclusion of process variables into the computation of time and size factors?
The inclusion of process variables into the computation of the time and size factors has been described by Salomone and Iribarren (1992) for analytical models and Salomone et al. (1994) when dynamic simulations are required. In this paper we adopted fermentation models that require dynamic simulations (the differential equations describing the fermentation are not analytically integrable), but the simplified analytical model for distillation presented by Zamar et al. (2000). For example, in the case of the prefermentor of the ethanol plant, the size factor is:
What is process control?
Process control is the ability to monitor and adjust a process to give a desired output. It is used in industry to maintain quality and improve performance. An example of a simple process that is controlled is keeping the temperature of a room at a certain temperature using a heater and a thermostat. When the temperature of the room is too low, the ...
How does variability affect process cost?
In most processes, the ability to control close to the desired set point and minimize variability has a significant impact on costs. If the set point needs to be raised to insure that a minimum value is met due to variability, the amount that the set point is raised over the desired value often result in wasted resources. For example, if a flow rate needs to be 10 gallons per minute to achieve a desired process result and the variability is +/- 1 gpm, the set point would need to be 11 gpm to ensure that the flow rate never fell below 10 gpm. This average of 1 gpm is then wasted product. If the variability was reduced to 0.1 gpm, the set point could be readjusted to 10.1 gpm which would result in a product savings for the operator.
Why is it important that each process is stable?
It is important that each process is stable as instability in one process will often cause other processes to become unstable. This instability is often called variability.
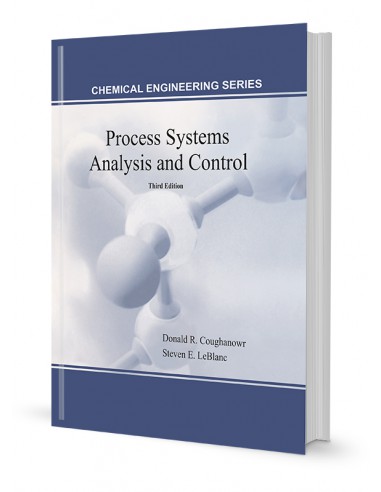